具有高适用性的挤出3D打印技术广泛应用于类器官生物制造、组织工程等领域。然而,传统挤出3D打印在墨水沉积轨迹上只可生产固定直径纤维,限制其难以设计制造复杂梯度多孔结构。
近日,中国科学院深圳先进技术研究院阮长顺研究员团队联合哈尔滨工业大学韩振宇教授团队,将医工交叉与融合,提出了变纤维直径3D打印技术,为仿生梯度结构构建提供新思路,相关成果发表在Nature Communications期刊,题为“Gradient matters via filament diameter-adjustable 3D printing”。该研究通过定制3D打印运动轨迹上的打印速度和打印高度,实现挤出3D打印纤维直径的精准控制,革新均匀纤维堆积的传统模式,实现梯度多孔结构的精准制造,为异质器官仿生构建提供新策略。
传统挤出3D打印采用平行切片方法,其在层内打印时保持恒定的打印速度V和打印高度H,沉积形成的纤维直径也保持恒定。尽管传统3D打印策略被普遍接受,并已成为制造均匀多孔结构的黄金标准,但固定的打印参数和恒定的纤维直径限制了其设计制造复杂梯度多孔结构。为突破传统3D打印策略的限制,研究团队基于体积守恒定律,通过定制运动轨迹上的打印速度和打印高度,实现各处纤维直径的精准控制,提出FDA-3DP(filament diameter-adjustable 3D printing)新策略。传统策略与FDA-3DP新策略所制造多孔梯度结构的最终效果,如视频中的Micro-CT数据所示。
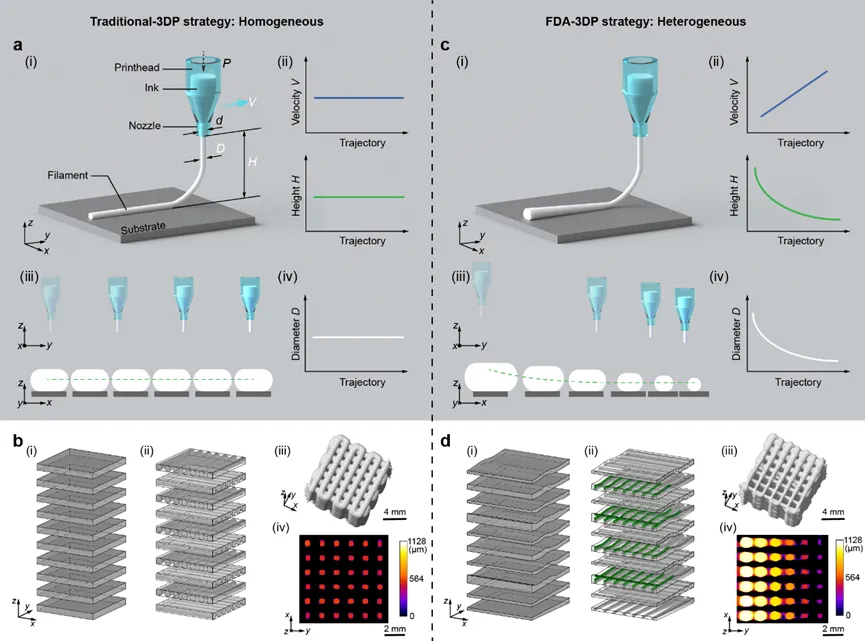
图1. 传统3D打印策略vs. FDA-3DP(filament diameter-adjustable 3D printing)新策略
FDA-3DP策略的关键参数为打印速度V和打印高度H。打印速度控制打印轨迹上所沉积纤维的直径,打印高度控制沉积纤维的质量和线性度。打印速度过慢会造成墨水堆积严重,打印高度过高将发生卷绳效应。
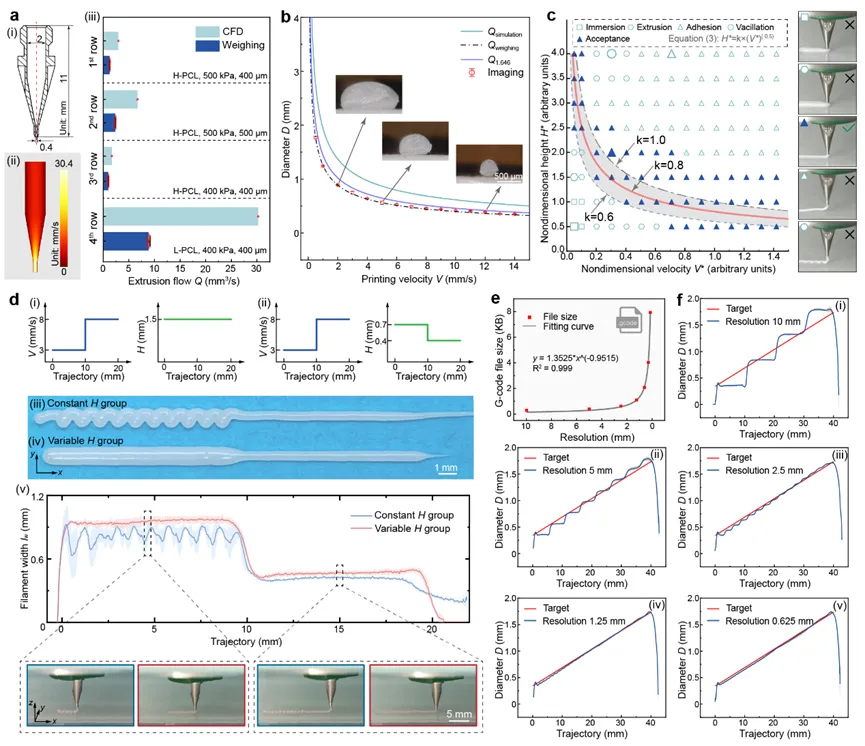
图2. FDA-3DP新策略的关键参数
为了证明该策略的有效性,研究团队在10mm尺寸的立方体内设计制造了水平梯度多孔结构。通过将打印轨迹与目标梯度相融合实现可控直径纤维的单层定制,并为了避免潜在的局部塌陷,提出固定直径纤维补偿机制。进而搭建“设计-制造”工作流程,重写制造代码G-codes,实现梯度多孔结构的挤出3D打印制造。Micro-CT重建数据证明通过该策略制造的水平梯度多孔结构与设计梯度模型的孔尺寸分布存在一致性。
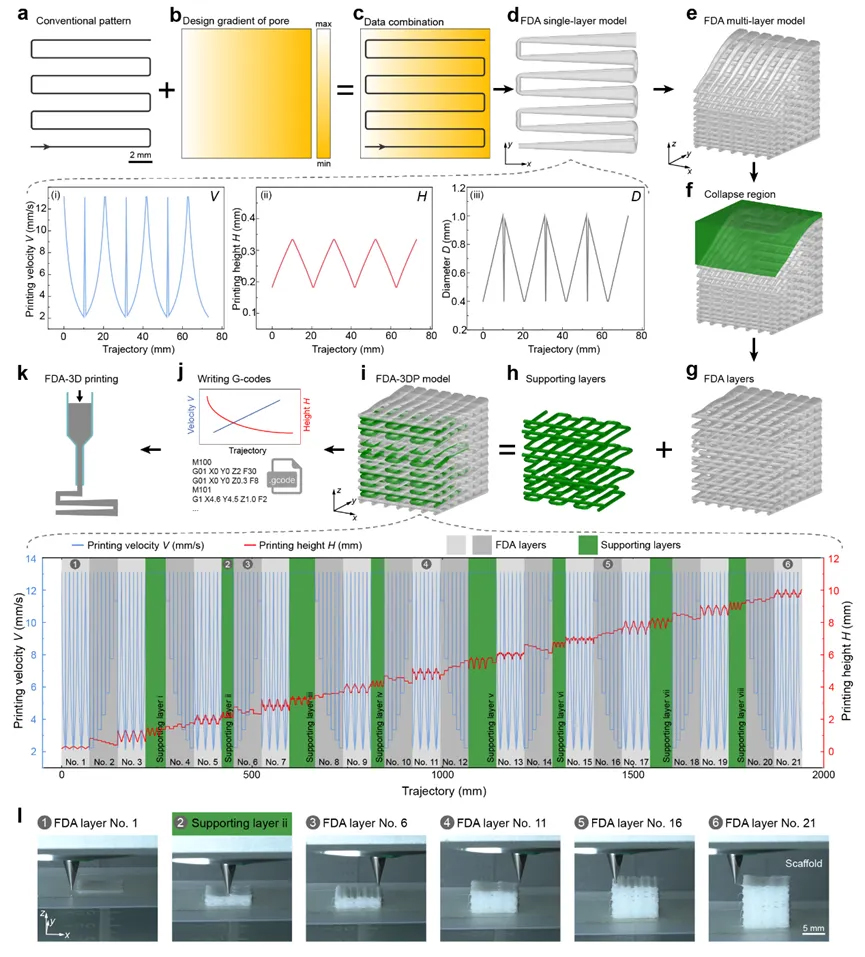
图3. 通过FDA-3DP新策略设计和制造水平梯度多孔结构
进一步,为了展示FDA-3DP策略的普适应,研究团队设计制造了轴向和包括点、线、面、体的径向梯度多孔结构。
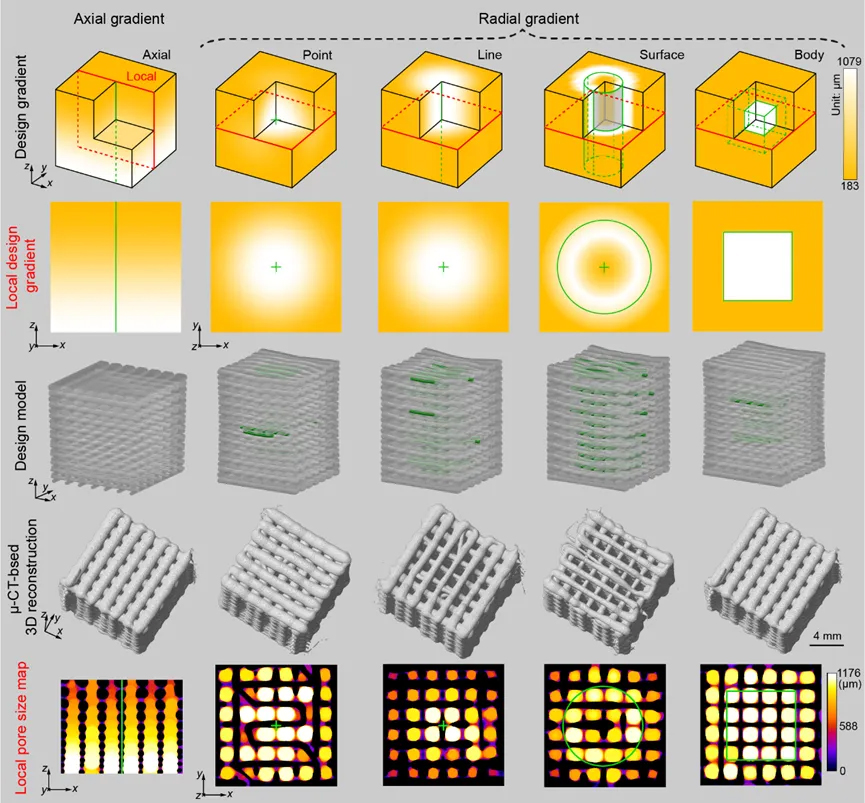
图4. 设计、制造和评估轴向和径向梯度多孔结构
为了探索展示FDA-3DP新策略的更深应用,研究团队设计制造了内嵌HIT字母(哈尔滨工业大学的首字母,Harbin Institute of Technology)的多孔梯度结构。结果显示HIT字母分别完成了在长方体内部的完全贯穿、居中隐藏和居中隐藏并逆时针旋转45°分布。此外,研究团队还在立方体内镶嵌V字母,探索了FDA-3DP策略在超结构领域定制局部力学性能的潜在应用。

图5. 高度可调孔尺寸的梯度结构(内嵌HIT字母和V字母)
该研究提出的FDA-3DP新策略突破了传统挤出3D打印技术难以加工复杂梯度多孔结构的难题,探索了其在组织工程与仿生器官制造(如骨、软骨、血管)、4D打印等领域的应用可行性。
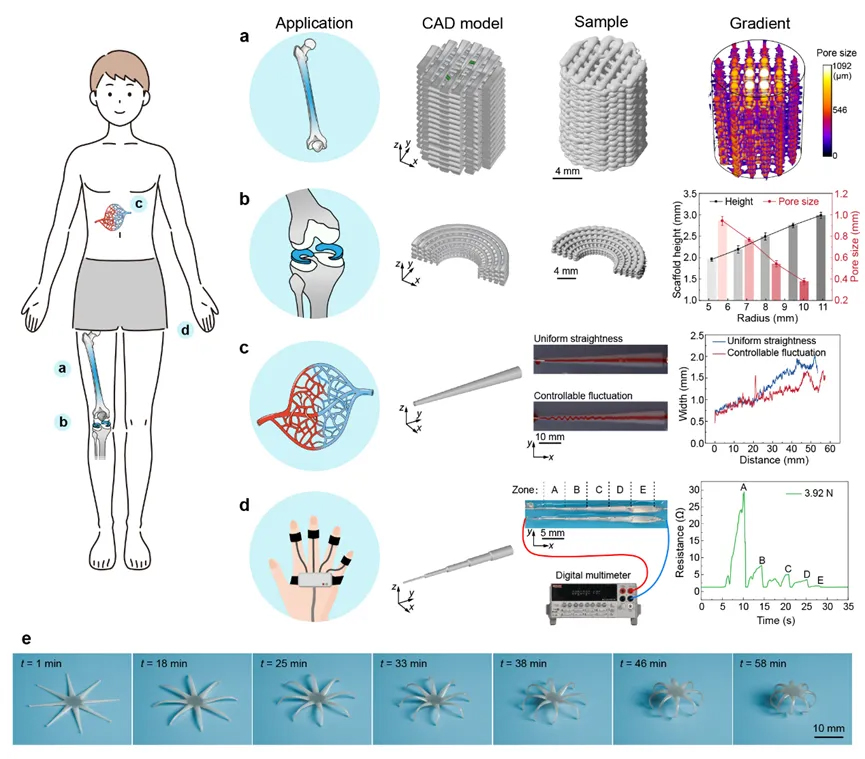
图6. FDA-3DP新策略应用探索
(来源:高分子科学前沿) |